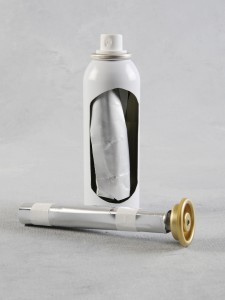
Bag-on-Valve (BoV) is a barrier packaging technology for companies with liquid or viscous products, looking to stand out from the competition.
Why not use traditional aerosols? In comparison to traditional aerosols, BoV separates your product from the propellant, keeping your product pure. BoV packaging is 100% recyclable, leaving a low ecological footprint. And most importantly, Bag-on-Valve is convenient and reliable for the end user.
Still not convinced? The following is a brief overview of how companies, like Aurena Laboratories manufacture and package Bag-on-Valve products.
How the Bag-on-Valve manufacturing process works
Standard BoV packaging covers a broad range from 30 to 500ml containers. Typically, BoV uses standard and fully recyclable aerosol aluminium cans with 1 inch can openings, together with foil-based packaging bags of multi-layer film laminates (for instance PET/ALU/OPA/PP). The bag is welded to the aerosol valve, which is crimped to the aerosol can in the filling process.
When the valve is crimped to the can the propellant, compressed air or nitrogen, is filled into the area between the bag and the can, keeping product and propellant separate at all times. This pressurising process is called under the cup gassing (UTC). The product in the bag encompasses 60 per cent of the can’s brim capacity, while the remaining 40 per cent is occupied by the propellant.
The benefits of BoV Manufacturing
-
Effective and safe filling process
-
Suitable for both liquid and viscous products
-
Can be used with standard actuators and aerosol cans
-
No need for flammable propellants
-
Hygienic and sterilizable
-
Less need for preservatives
Is your product right for a BoV can?
Due to the low permeability rate, BoV is also compatible with commercially available liquefied propellants. These propellants make good choices for products that call for a steady dispensing rate over the life of the can, such as post-foaming gels and creams.
Almost all fluids and more viscous products can be filled into a BoV-system as long as the product’s viscosity is low enough to get it through the valve stem. However, the system does not work well with products that need to be shaken before use, since the bag is filled and doesn’t improve mixing when shaken.
Bag-on-Valve Manufacturers and Suppliers
BoV-system, used to make the final products, are manufactured and sold by international companies like Aptar Group, Lindal Group and Coster. Leading suppliers of the special aerosol filling machines needed to fill BoV products are MBC Aerosol (USA) and Pamasol (Switzerland).
*For more information about Bag-on-Valve suppliers, visit our suppliers page.
The future of Bag-on-Valve manufacturing
In the near future, we can expect new innovative ways to manufacture BoV with higher speed manufacturing, laminate developments for more compatibility and decreasing the amount of laminate layers, among other steps in developing the next generation of Bag-on-Valve systems.
Ready to start using Bag-on-Valve for your healthcare products? Contact us today to learn more.